 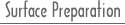
Common Surfaces and their Suitability for Adhesive Bonding
A critical factor in the success of any adhesive bond is the condition of the assembly surfaces being joined. Every assembly surface has unique characteristics, either inherent in its material make up, such as aluminum oxidization; or added to it during manufacturing, such as rust inhibitors. This guide provides an overview of several common materials and their suitability for adhesive bonding. Consult a
Cyabond® representative for a complete assessment of your assembly surfaces and determination of the best
Cyabond® adhesive for your specific application.
Aluminum and its Alloys
- Surface appears clean but has a thin oxide film that weakens the bond between the true aluminum surface and the
adhesive.
- Some oxide films may be stable enough to provide a strong bond without any surface preparation. This is the exception. Have
Cyabond® evaluate aluminum surface bonds.
- Oxide films form immediately, even after surface treatment. Surface bonding must take place as soon as possible to achieve maximum adhesion
strength.
Conventional Steel Alloys
- Mild steel alloys typically present surfaces readily able to be
bonded.
Zinc-plated Steel
- Presents an oxide film that may weaken the bond between the true steel and the
adhesive.
- Zinc plating may separate from the steel surface as a result of the
adhesive.
- May require chemical treatment to eliminate the zinc separation from the steel
sheet.
Treated Zinc-plated Steel
- The treated surface is both unsuitable and unreliable for adhesive
bonding.
- Certain chemical treatment methods can present workable bonding
surfaces.
PVC-coated Steel
- Structural joints cannot be formed on the PVC cladded surfaces of mild steel. Toughened acrylic adhesives will provide good adhesion to the PVC
surface.
Painted Steel Panels
- Structural joints cannot be formed on the painted surfaces of steel
panels.
- Several
Cyabond® adhesives will provide good adhesion to painted steel panels.
- Maximum adhesion will be achieved by those
Cyabond® adhesives that will flex with the bending of thin sheet
panels.
Stainless Steel Alloys
-
Cyabond® toughened acrylic and 1-part epoxy adhesives bond well to these
alloys.
- Depending on the application, chemical surface treatment may be
necessary.
- Surface preparation with abrasion and a solvent wipe is suitable in most
cases.
Thermoset GRPs
-
Cyabond® toughened acrylic, 1-part epoxy, and polyurethane adhesives bond well to these
surfaces.
- Surface activated toughed acrylics may not provide suitable gap filling ability for large structural
applications.
Acrylic-faced Thermoset GRPs
- Structural joints cannot be formed on the acrylic face of these
surfaces.
-
Cyabond® pre-mixed toughened acrylics will provide the maximum adhesion to the acrylic faced
surface.
- The adhesive and the initiator of 2-part acrylic adhesives, in their liquid form, will cause stress cracking on the acrylic face after prolonged
exposure.
Wood-faced Thermoset GRPs
- Wood-faced Thermoset GRPs typically present surfaces readily able to be
bonded.
- Several
Cyabond® adhesives will provide good adhesion to these surfaces.
CRFPs
- These structural composites, typically epoxy-based, bond well with a variety of
Cyabond® adhesives - particularly the toughened acrylics.
ABS
-
Cyabond® pre-mixed toughened acrylics will provide the maximum adhesion to these
surfaces.
- The adhesive and the initiator of 2-part acrylic adhesives, in their liquid form, will cause stress cracking on the surface after prolonged
exposure.
Nylon
- Extensive surface treatment may be necessary to achieve suitable
bonding.
Polyolefin
- Extensive surface treatment may be necessary to achieve suitable
bonding.
Polyurethane
- Presents a difficult surface for effective adhesive bonding.
-
Cyabond® polyurethane and toughened acrylic adhesives bond well to this
surface.
PVCs
-
Cyabond® pre-mixed toughened acrylics will provide the maximum adhesion to both rigid and flexible PVC surfaces - particularly in harsh
environments.
-
Cyabond® cyanoacrylate and solvent-based adhesives will also provide a suitable bond to both rigid and flexible PVC
surfaces.
Common Surface Preparation Guidelines
Although many of
Cyabond® 's industrial adhesives provide excellent bonding to "as received" surfaces, proper surface preparation will dramatically improve adhesion strength and bond performance. A properly prepared component will present a surface that is uniformly clean, mechanically sound, and correctly textured. A prepared surface will ensure strong and durable bonds; particularly when harsh usage environments are present. This guide provides an overview of several surface preparation methods. Consult a
Cyabond® representative for a complete assessment of your assembly surfaces and determination of the best surface preparation method for your specific
application.
Surface Preparation: Solvents
- If possible, remove surface oil or grease with an aqueous-based
cleanser.
- If aqueous-based cleansers are ineffective, isopropyl alcohol is
recommended.
- If isopropyl alcohol is ineffective, solvents such as acetone or methyl ethyl ketone can be
used.
- It is recommended that the surface material first be tested as certain thermoplastics may crack or dissolve when reacting to various
solvents.
Surface Preparation: Mechanical
Mechanical scarification is a process of slightly roughening the surface of the component to be bonded. The surface roughness should be kept to less than 0.1 microns (0.004 millimeters) to reduce the possibility of small contaminants or air bubbles becoming trapped in the roughened surface and degrading the bond performance. Scarification is typically done with either an abrasion or a blasting
process.
Abrasion:
- Abrade using 45 to 106 micron grit or a three-dimensional, non-woven abrasive
fabric.
- Abrading can be done as either a wet or a dry process. If doing wet abrading, use only media designated as
water-resistant.
- When preparing aluminum surfaces always use the wet method to prevent the oxide pores from clogging with abraded
contaminants.
- Proper surface condition has been achieved when the surface can be immersed in clean water, and when removed a water film remains unbroken for 30 seconds. Do not use iron- or steel-based grits on aluminum, copper, or stainless steel
components.
Dry Blasting:
- Typically used on metallic components. May also be used on heavy-duty
plastics.
- Blast using 45 to 106 micron grit until the surface is uniform in cleanliness and
texture.
Wet Blasting:
- Typically used on small metallic components.
- Blast using 1000 mesh grit suspended in either water or steam.
- In the event a system uses water-soluble additives, consult the system manufacturer to eliminate contamination of the surface by the
additives.
Surface Preparation: Non-mechanical
Non-mechanical surface preparation methods are typically for only high volume plastic or composite component production applications. Non-mechanical surface preparation modifies the chemical characteristics of the component's surface to an optimum condition for adhesive bonding.
Gas Flame Oxidizing:
- Economical and effective method of preparing plastic or composite
surfaces.
- Rapidly adapts to changes in component topography.
Plasma Discharge: (Also known as Corona Discharge)
- Economical and effective method of preparing plastic or composite
surfaces.
- Best suited for components with simple, or flat topography.
Plasma Chamber:
- Utilizes a discharge chamber to process large volume component
batches.
- Best suited for batches with complex, or multiple component shapes.
- Requires greater initial capital investment; provides greater volume and part type processing than other non-mechanical surface preparation
processes.
Laser:
- Can be used for metal and plastic component surfaces.
- Requires extensive system design, and calibration. Consult with a
Cyabond® representative to evaluate laser surface preparation for your
application.
|
 |
|